Meet our talented craftspeople
When Siiri Nenonen, 23, started working as an assembler of Secto Design shades a few years ago, she kept dropping slats on the floor on her first days on the job, whereas in the hands of a more experienced colleague, the shades seemed to take shape by themselves. It took some time for her fingers to grow accustomed to handling birchwood.
“Assembling a shade requires some dexterity as you make sure that every nail is in the right angle and the slats are evenly spaced. You need to have a visual eye to see what looks right and what does not,” says Siiri at her workstation in the bright assembly hall of the Secto Design factory.
Slats for the Octo lamp are waiting on her desk. Before Siiri starts assembling them into a shade, she inspects each slat individually and cleans and sands them smooth. She also makes sure that only high-quality slats end up being used in the lamp.
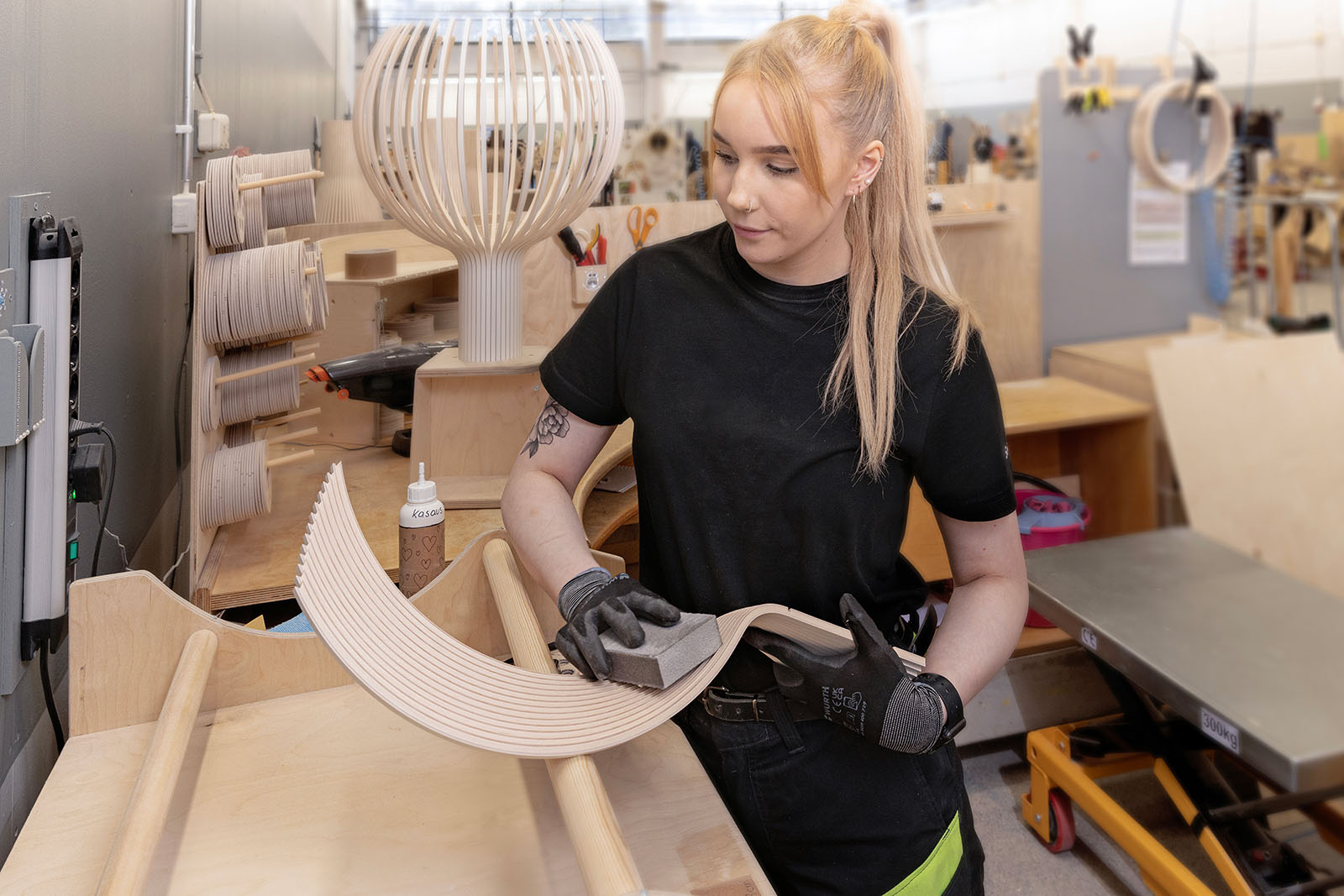
“I enjoy cleaning the slats before I start assembling them into a shade. It feels satisfying to sand off the rough slats to make them smooth,” says shade assembler Siiri Nenonen.
Secto Design has approximately 30 lamp models and each and every model requires a unique set of skills from the assembler. With meticulous attention to detail, the quality of the work remains high and no material goes to waste.
“Assembling a shade is similar to doing crafts. I feel a sense of pride every time I finish a shade and see how fine it looks. When I see a Secto Design lamp in a restaurant, for instance, I always go and see if it is one of the lamps I have made.”
Several other assemblers also work in the same hall as Siiri. Assembled shades are placed next to the workstations, waiting to be sanded smooth. The air is filled with lively chatter and the sound of the sanding machine. Working on the other side of the hall is Tuula Järvinen, 65, who uses the word ‘love’ when she talks about Secto Design lamps.
“I sent in an open application six years ago saying that a granny is looking for a job, and then the granny got the job. I immediately fell in love with assembling these shades and the lamps themselves. I really do not want to retire from this job, despite my age,” says Tuula with a smile, picking up slats for the next shade.
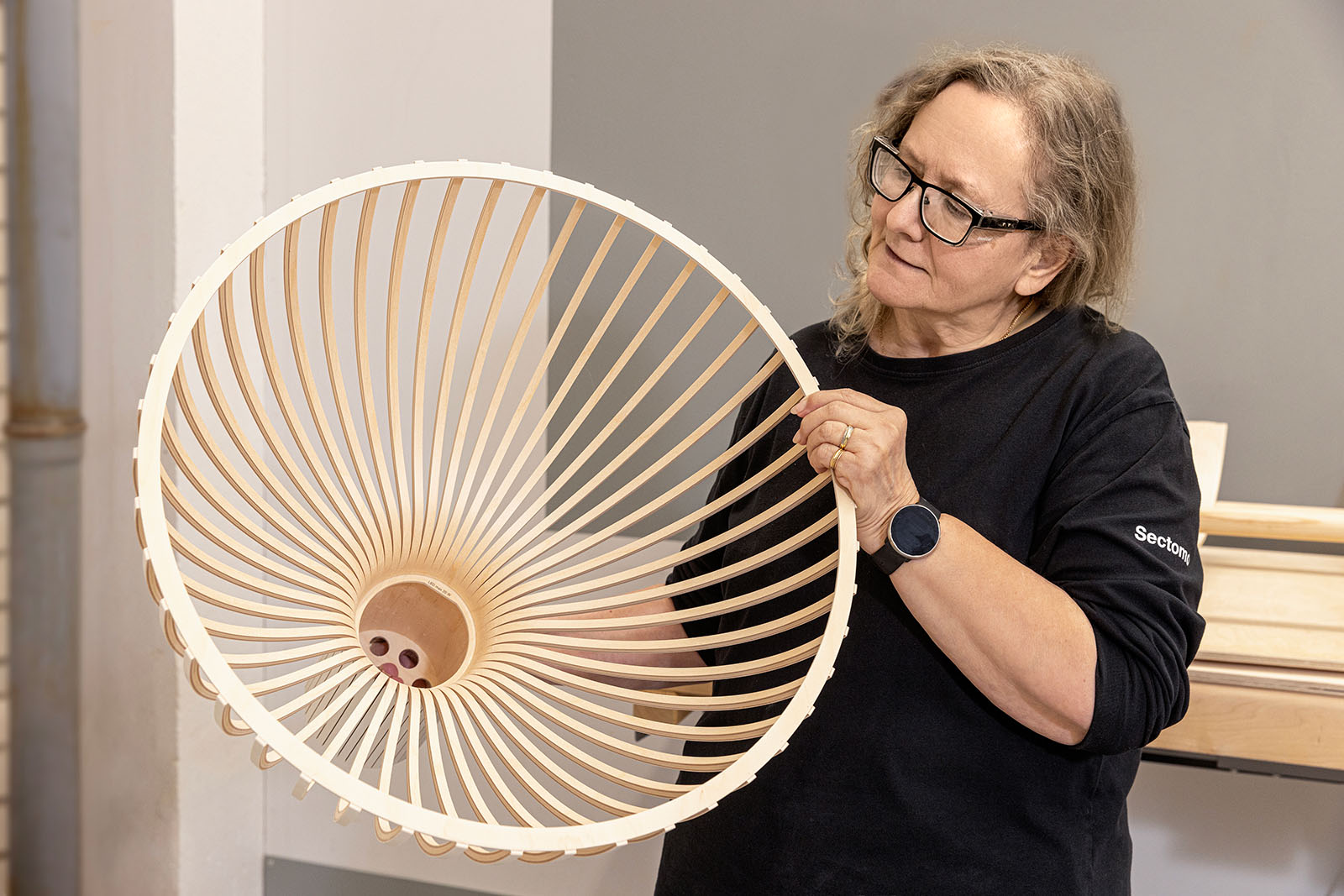
Shade assembler Tuula Järvinen often spots Secto Design lamps on Grand Designs and other TV programmes. “Whenever I finish a shade, I cannot help but think how pretty they are.”
Before making it to the desks of Siiri and Tuula, the slats have passed through many skilled hands at the Secto Design factory. These hands include those of Jouko Vinkka, 58, who operates the sanding machine.
“Manufacturing lamps is a clean and precise job that is perfect for my pedantic nature. I am more precise than the sun. The sanding machine, for example, can be adjusted with an accuracy of one hundredth of a millimetre. I take pleasure in making sure that everything is just right,” says Jouko.
Jouko also operates the water jet cutter and works in the ring workshop, manufacturing the rings that are the essential cohesive elements of the Secto Design lamps.
Acquired by the factory in 2020, the water jet cutter turns water into an environmentally friendly, efficient and accurate cutting method. Although the machine does the actual cutting, Jouko is there to ensure that the settings are correct and the quality is top-notch.
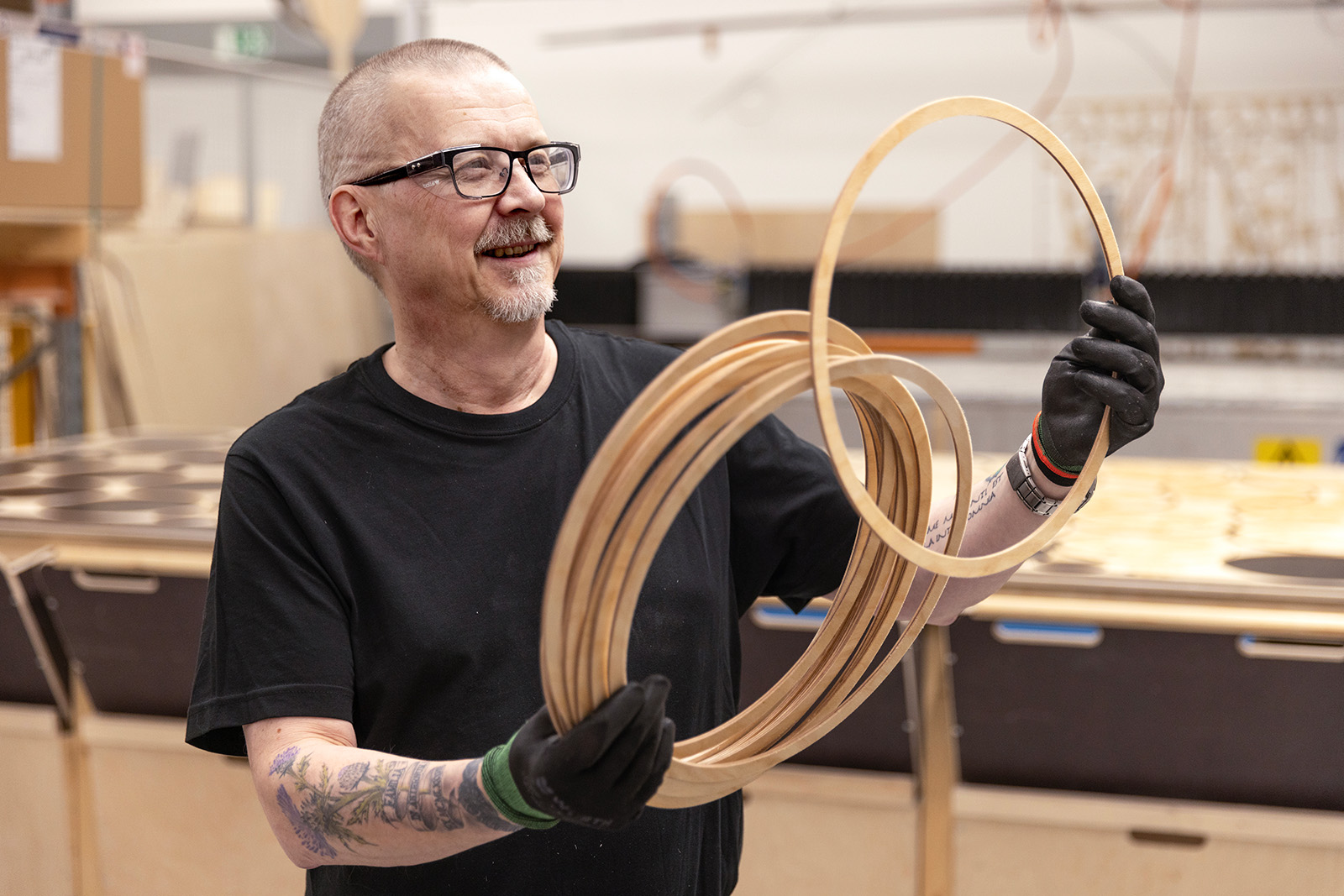
Jouko Vinkka has had a long career of working with various light and heavy machinery and knows them down to the smallest detail. “I understand the inner workings of machines,” he says.
Quality is a word that often comes up in conversations with Jouko and the other craftspeople at Secto Design. An essential part of craftsmanship is understanding the material and bringing out its properties in the best possible way. All Secto Design lamps are made from premium Finnish birch, which is a renewable, carbon-binding material. It is also a natural material with a will of its own.
“It is important to constantly monitor the quality of the material and notice any variations. Everyone here takes pride in their work. The quality that leaves our door is the best there is,” says Jouko.
Otto Ruuttula, 30, agrees with Jouko. As a multi-skilled person, he not only operates the water jet cutter, but also assembles shades and services woodworking tools and machines.
“I feel valued at work and know that my ideas and views matter. For example, I have built additional shelves on an aerial work platform to make storing tools easier. I like the fact that we can develop our working methods and put our ideas forward,” Otto says.
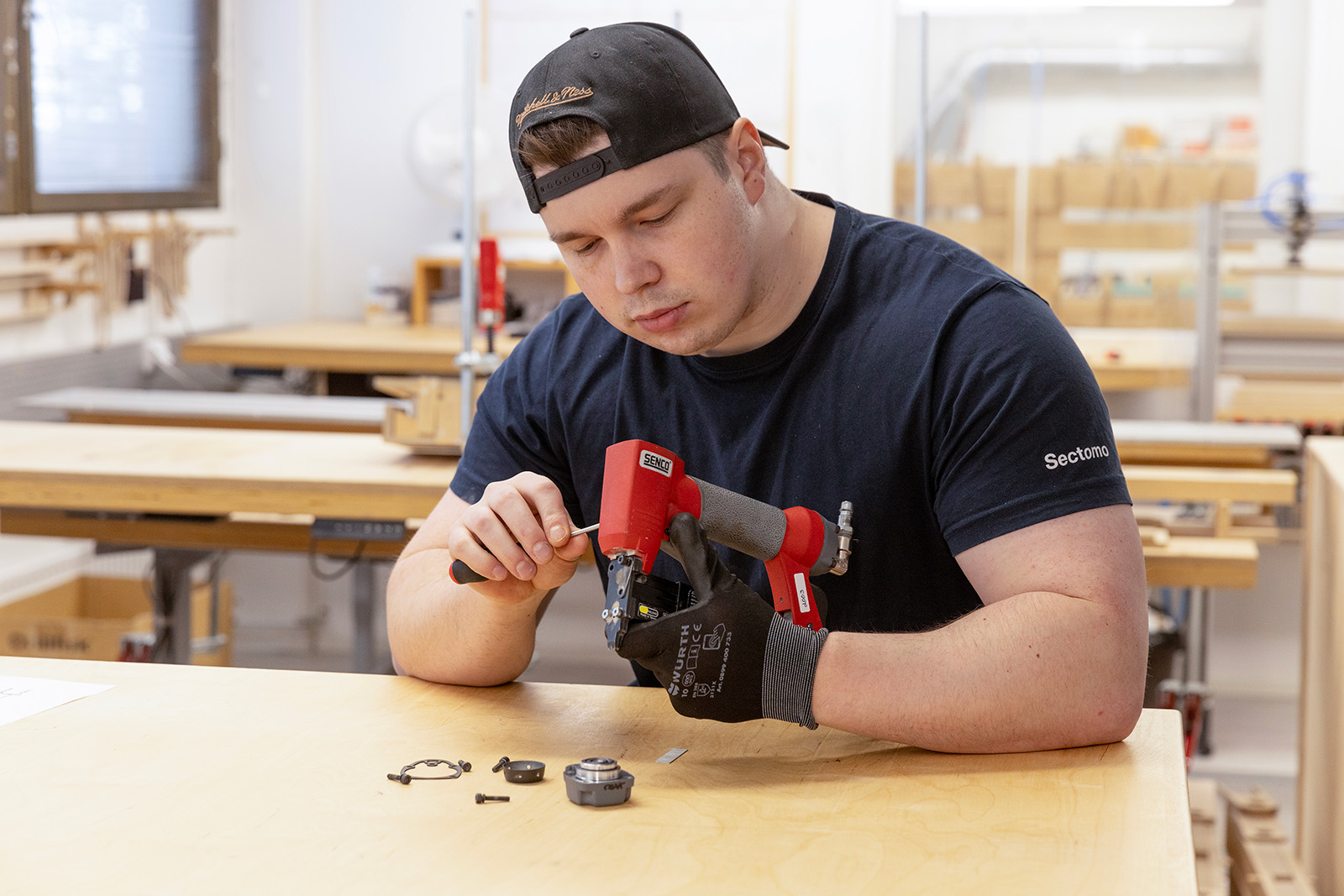
In addition to his other duties, Otto Ruuttula is skilled at servicing and repairing the tools and machines at the factory. “I enjoy working here as I can constantly develop myself and my skillset.”